Home > Certifications > Supply Chain Management Series > Certified International Supply Chain Professional (CISCP, Level 1) >
Certified International Supply Chain Professional (CISCP, Level 1)
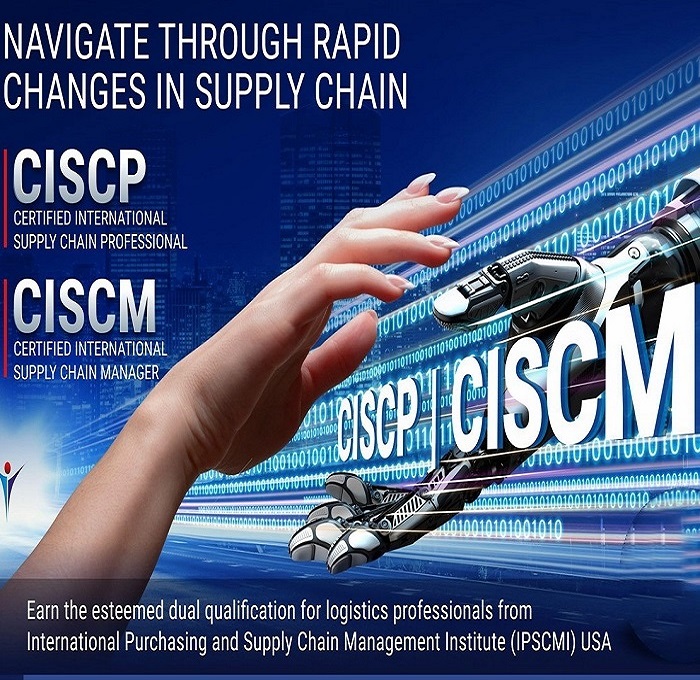
Certified International Supply Chain Professional (CISCP, Level 1)
The Certified International Supply Chain Professional (CISCP) is the Entry Level Certification of IPSCMI Supply Chain Management Series. CISCP covers definitions and basic supply chain management terminology. It explores the functions of supply chain management and logistics, supply chain decisions, supply chain designs, global supply chains and virtual supply chains. It also covers the relationship between supply chain/logistics strategy and the structure of the organization; and the influence of organizational structure on performance.
Introduction
This Certification Program is a core certification program of the International Purchasing And Supply Chain Management Institute.
This program offers the designation of CISCP (Certified International Supply Chain Professional, Entry Level) to candidates who demonstrate their understanding of the fundamentals of the profession through the successful completion of rigorous professional certification examinations based upon the INTERNATIONAL SUPPLY CHAIN MANAGEMENT BODY OF KNOWLEDGE (ISCMBOK).
This program offers the designation of CISCP (Certified International Supply Chain Professional, Entry Level) to candidates who demonstrate their understanding of the fundamentals of the profession through the successful completion of rigorous professional certification examinations based upon the INTERNATIONAL SUPPLY CHAIN MANAGEMENT BODY OF KNOWLEDGE (ISCMBOK).
Certification Objectives
Upon completion of this certification program, students should be able to:
- Define supply chain, supply chain management, distribution channel, demand management, distribution management, and logistics management.
- Describe the different types of supply chains.
- List and describe the various components of a supply chain.
- Explain the role of information systems and information technology in supply chain management
- Describe the functions of supply chain management and logistics
- Explain the motivations for supply chain management.
- Explain how to make supply chain decisions
- Describe different supply chain designs.
- Explain global supply chains and virtual supply chains,
- Explain the relationship between supply chain/logistics strategy and the structure of the organization
- Describe how organizational structure affects performance.
- Explain the changing appearance of logistics and supply chain organizations within the firm.
- Explain the purchasing, transportation, inventory management, production planning and control, physical distribution, and MIS functions as they relate to Supply Chain Management.
- Describe the process of Supply Chain Management Performance Measurement.
- Describe, in general terms, the future of Supply Chain Management.
Modules for CISCP Certification
Module 1 Introduction to Logistics and Supply Chain Management
The module covers definitions and basic terminology, including supply chain, supply chain management, distribution channel, demand management, distribution management, and logistics management. It explores the functions of supply chain management and logistics, motivations for supply chain management, logistics concerns, goals of logistics, the logistics “Bill of Rights”, the marketing-logistics relationship, supply chain decisions, supply chain designs, global supply chains and virtual supply chains, support for international carriers, international trade agreements, components of logistics management, logistics in the modern environment, functions associated with supply chain management, the components of logistics, functions of traffic management, major advantages of the various transportation modes, the controllable elements of a logistics system, major categories of service complaints as they relate to logistics, and cost trade-offs in logistics. Also covered are the relationship between supply chain/logistics strategy and the structure of the organization; the influence of organizational structure on logistics performance; and the changing appearance of logistics and supply chain organizations within the firm.
Module 2 Relationship between Purchasing and Supply Chain Management
The Module covers three major areas. The first topic covers a comparison of the types of transportation for domestic and international shipments, how to make routing decisions based on the goals of the firm, the different terms of sale/purchase and which best protects the firm versus which is commonly used, and the consequences that are associated with each type of logistics decision in terms of cost effectiveness and ability to meet demand, (focusing on the cost of logistics). The second topic covers purchasing management, primarily from a domestic (generic) perspective. Purchasing is described as a subset of Logistics/Supply Chain Management and Materials Management. The four procurement (preaward) processes and the two contract administration (postaward) processes are discussed and explained in detail (Procurement planning: determining what to procure and when, Solicitation planning: documenting product requirements and identifying potential sources, Solicitation: obtaining quotations, bids, offers, or proposals as appropriate, Source selection: choosing from among potential suppliers, Contract administration: managing the relationship with the supplier, and Contract close-out: completion and settlement of the contract). Methods of procurement and contract types are addressed in summary detail. The third topic covers the special characteristics of international purchasing, focusing on those issues which make international purchasing different from domestic purchasing. International contract law, INCOTERMS, documentation, and payments are all addressed.
Module 3 the Domestic and International Transportation Systems
The Module provides an appreciation of the macroeconomic and microeconomic roles of transportation; the characteristics of various transportation modes; and understanding of the economics of movement; and covers the changing environment in which transportation operates in the U.S. It also covers transportation’s critical role in supply chain operations; how the transportation system is analyzed; an explanation of how transportation operations are managed; and how information coordinates the flow of materials and goods. The Module also provides an understanding of the escalating importance of international logistics as crucial tools for competitiveness; explains the difference between materials management and physical distribution; provides an understanding of why international logistics is more complex than domestic logistics; how the transportation infrastructure in host countries often dictates the options open to the international manager; and why inventory management is crucial for international success. It also covers globalization and business competitiveness; transportation requirements of competitive firms; transportation sector response to competitiveness; information requirements; and data needs (counting the emerging freight sector). Extensive treatment is given to International Commercial Terms (Incoterms).
Module 4 Production Planning and Scheduling
This Module covers the overall approach to producing goods and services and explains the various production-related decisions, including that of capital intensity, process flexibility, vertical integration, and customer involvement. The different production methodologies, including project, mass, batch, and continuous, are covered in detail. Production planning and control methodologies are discussed in detail. Material requirements planning (MRP), manufacturing resource planning (MRPII) and just-in-time (JIT) systems are discussed in the context of materials planning. Production scheduling is discussed in detail, to the specifics of when labor, equipment, and facilities are needed to produce a product or provide a service. Coverage will also be given to a discussion of disposal as a growth industry that provides many marketing opportunities, and recognition will be given to an understanding that product disposition is an increasingly important area for public policy. The Module will discuss some of the practical implications that disposition has for managers, explain the differences between voluntary and involuntary disposition, describe the social, individual and situational factors that affect disposition choices, and provide an understanding of how disposition provides key insights into consumption behavior. Also covered are an understanding of the location problem; the problems related to site selection; the characteristics of a median location; single facility considerations, including center of gravity, exact location, and use of the minimax rule; multiple facility considerations, including location allocation and economies of scale, selection of dynamic locations, and the production-inventory-transportation relationship. Finally, a discussion of “Green Logistics” will explain why and how waste can be minimized in order to minimize the problem of “Reverse Logistics”.
Module 5 Inventory Management and Warehousing
The Module covers inventory management in detail. Specifics include the fundamental purpose of maintaining inventory; an understanding of the benefits and costs of inventory; an examination of the tradeoffs present among inventory, customer service and other functional costs in logistics; and the rationing methods and inventory performance measurement. Special attention is given to an understanding of the importance of coordinated flows of inventory through supply chains; the impact of effective inventory management upon the return on assets (ROA) for a company; the role and importance of inventory in the economy and why inventory levels have declined relative to Gross Domestic Product (GDP); an awareness of inventory management techniques; practical insight toward common management tools; and practice with the application of inventory management decision tools. Attention is given to understanding how demand influences replenishment model selection; the strategic, operational and performance differences between PUSH and PULL inventory systems; and awareness of the shift from PUSH to PULL systems and reasons for the shift.
Warehousing is discussed in detail. Specifics include the modern purpose and function of warehouses; warehouse activities; warehouse strategies; and changes in the operational scope and capabilities of warehouses; fundamental warehouse decisions; warehouse and materials handling operations; and the functionality and requirements of product packaging.
Module 6 Physical Distribution Management
This Module is designed to provide students with an in-depth understanding of the operational, financial and managerial aspects of the physical distribution of industrial goods.
Components of Physical Distribution Management include:
1. Order processing;
2. Stock levels or inventory;
3. Warehousing;
4. Transportation.
5. Marketing Channels (distribution intermediaries)
The Module covers the critical importance of outbound-to-customer logistics and supply chain management systems and the components of those systems. It requires students to appreciate the growing need for effective demand management as part of a firm’s overall logistics and supply chain expertise; know the types of forecasts that may be needed, and understand how collaboration among trading partners will help the overall forecasting and demand management process; identify the key steps in the order-fulfillment process, and understand how effective order management can create value for a firm and its customers; realize the meaning of customer service, and understand its importance to logistics and supply chain management; understand the difference between logistics and marketing channels, and understand that goods may reach their intended customer via a number of alternative channels of distribution; and understand how to develop and manage marketing channels. Inventory, Warehousing, and Transportation are covered in previous modules (5, 5, and 3, respectively).
Module 7 Logistics Structure and Productivity, Quality Management, Statistical Process (Quality) Control, E-Commerce (E-Logistics) and Third Party Logistics
The Module covers the relationship between supply chain/logistics strategy and the structure of the organization; the influence of organizational structure on supply chain/logistics performance; and the changing appearance of logistics and supply chain organizations within the firm. Special attention is given to methods of increasing the productivity of supply chain management and logistics, including E-commerce/E-Logistics, the techniques needed to improve the efficiency of inventory investment; the reconciliation of logistics needs with enterprise resource planning (ERP) systems; the exploitation of cost and service opportunities provided by third-party logistics services; the exploitation of opportunities in integrated package design; support programs that will reduce the driver shortage; the reformation of public policy to improve productivity; and focus of transportation policy on competition instead of protection. Attention is given to reduction of trucking costs with safe, longer and heavier highway vehicles; maritime reform; avoidance of railroad reregulation; and reform of the Jones Act to improve global competitiveness. Quality Management is discussed in detail, including the techniques of Statistical Process Control and Total Quality Management.
The module covers definitions and basic terminology, including supply chain, supply chain management, distribution channel, demand management, distribution management, and logistics management. It explores the functions of supply chain management and logistics, motivations for supply chain management, logistics concerns, goals of logistics, the logistics “Bill of Rights”, the marketing-logistics relationship, supply chain decisions, supply chain designs, global supply chains and virtual supply chains, support for international carriers, international trade agreements, components of logistics management, logistics in the modern environment, functions associated with supply chain management, the components of logistics, functions of traffic management, major advantages of the various transportation modes, the controllable elements of a logistics system, major categories of service complaints as they relate to logistics, and cost trade-offs in logistics. Also covered are the relationship between supply chain/logistics strategy and the structure of the organization; the influence of organizational structure on logistics performance; and the changing appearance of logistics and supply chain organizations within the firm.
Module 2 Relationship between Purchasing and Supply Chain Management
The Module covers three major areas. The first topic covers a comparison of the types of transportation for domestic and international shipments, how to make routing decisions based on the goals of the firm, the different terms of sale/purchase and which best protects the firm versus which is commonly used, and the consequences that are associated with each type of logistics decision in terms of cost effectiveness and ability to meet demand, (focusing on the cost of logistics). The second topic covers purchasing management, primarily from a domestic (generic) perspective. Purchasing is described as a subset of Logistics/Supply Chain Management and Materials Management. The four procurement (preaward) processes and the two contract administration (postaward) processes are discussed and explained in detail (Procurement planning: determining what to procure and when, Solicitation planning: documenting product requirements and identifying potential sources, Solicitation: obtaining quotations, bids, offers, or proposals as appropriate, Source selection: choosing from among potential suppliers, Contract administration: managing the relationship with the supplier, and Contract close-out: completion and settlement of the contract). Methods of procurement and contract types are addressed in summary detail. The third topic covers the special characteristics of international purchasing, focusing on those issues which make international purchasing different from domestic purchasing. International contract law, INCOTERMS, documentation, and payments are all addressed.
Module 3 the Domestic and International Transportation Systems
The Module provides an appreciation of the macroeconomic and microeconomic roles of transportation; the characteristics of various transportation modes; and understanding of the economics of movement; and covers the changing environment in which transportation operates in the U.S. It also covers transportation’s critical role in supply chain operations; how the transportation system is analyzed; an explanation of how transportation operations are managed; and how information coordinates the flow of materials and goods. The Module also provides an understanding of the escalating importance of international logistics as crucial tools for competitiveness; explains the difference between materials management and physical distribution; provides an understanding of why international logistics is more complex than domestic logistics; how the transportation infrastructure in host countries often dictates the options open to the international manager; and why inventory management is crucial for international success. It also covers globalization and business competitiveness; transportation requirements of competitive firms; transportation sector response to competitiveness; information requirements; and data needs (counting the emerging freight sector). Extensive treatment is given to International Commercial Terms (Incoterms).
Module 4 Production Planning and Scheduling
This Module covers the overall approach to producing goods and services and explains the various production-related decisions, including that of capital intensity, process flexibility, vertical integration, and customer involvement. The different production methodologies, including project, mass, batch, and continuous, are covered in detail. Production planning and control methodologies are discussed in detail. Material requirements planning (MRP), manufacturing resource planning (MRPII) and just-in-time (JIT) systems are discussed in the context of materials planning. Production scheduling is discussed in detail, to the specifics of when labor, equipment, and facilities are needed to produce a product or provide a service. Coverage will also be given to a discussion of disposal as a growth industry that provides many marketing opportunities, and recognition will be given to an understanding that product disposition is an increasingly important area for public policy. The Module will discuss some of the practical implications that disposition has for managers, explain the differences between voluntary and involuntary disposition, describe the social, individual and situational factors that affect disposition choices, and provide an understanding of how disposition provides key insights into consumption behavior. Also covered are an understanding of the location problem; the problems related to site selection; the characteristics of a median location; single facility considerations, including center of gravity, exact location, and use of the minimax rule; multiple facility considerations, including location allocation and economies of scale, selection of dynamic locations, and the production-inventory-transportation relationship. Finally, a discussion of “Green Logistics” will explain why and how waste can be minimized in order to minimize the problem of “Reverse Logistics”.
Module 5 Inventory Management and Warehousing
The Module covers inventory management in detail. Specifics include the fundamental purpose of maintaining inventory; an understanding of the benefits and costs of inventory; an examination of the tradeoffs present among inventory, customer service and other functional costs in logistics; and the rationing methods and inventory performance measurement. Special attention is given to an understanding of the importance of coordinated flows of inventory through supply chains; the impact of effective inventory management upon the return on assets (ROA) for a company; the role and importance of inventory in the economy and why inventory levels have declined relative to Gross Domestic Product (GDP); an awareness of inventory management techniques; practical insight toward common management tools; and practice with the application of inventory management decision tools. Attention is given to understanding how demand influences replenishment model selection; the strategic, operational and performance differences between PUSH and PULL inventory systems; and awareness of the shift from PUSH to PULL systems and reasons for the shift.
Warehousing is discussed in detail. Specifics include the modern purpose and function of warehouses; warehouse activities; warehouse strategies; and changes in the operational scope and capabilities of warehouses; fundamental warehouse decisions; warehouse and materials handling operations; and the functionality and requirements of product packaging.
Module 6 Physical Distribution Management
This Module is designed to provide students with an in-depth understanding of the operational, financial and managerial aspects of the physical distribution of industrial goods.
Components of Physical Distribution Management include:
1. Order processing;
2. Stock levels or inventory;
3. Warehousing;
4. Transportation.
5. Marketing Channels (distribution intermediaries)
The Module covers the critical importance of outbound-to-customer logistics and supply chain management systems and the components of those systems. It requires students to appreciate the growing need for effective demand management as part of a firm’s overall logistics and supply chain expertise; know the types of forecasts that may be needed, and understand how collaboration among trading partners will help the overall forecasting and demand management process; identify the key steps in the order-fulfillment process, and understand how effective order management can create value for a firm and its customers; realize the meaning of customer service, and understand its importance to logistics and supply chain management; understand the difference between logistics and marketing channels, and understand that goods may reach their intended customer via a number of alternative channels of distribution; and understand how to develop and manage marketing channels. Inventory, Warehousing, and Transportation are covered in previous modules (5, 5, and 3, respectively).
Module 7 Logistics Structure and Productivity, Quality Management, Statistical Process (Quality) Control, E-Commerce (E-Logistics) and Third Party Logistics
The Module covers the relationship between supply chain/logistics strategy and the structure of the organization; the influence of organizational structure on supply chain/logistics performance; and the changing appearance of logistics and supply chain organizations within the firm. Special attention is given to methods of increasing the productivity of supply chain management and logistics, including E-commerce/E-Logistics, the techniques needed to improve the efficiency of inventory investment; the reconciliation of logistics needs with enterprise resource planning (ERP) systems; the exploitation of cost and service opportunities provided by third-party logistics services; the exploitation of opportunities in integrated package design; support programs that will reduce the driver shortage; the reformation of public policy to improve productivity; and focus of transportation policy on competition instead of protection. Attention is given to reduction of trucking costs with safe, longer and heavier highway vehicles; maritime reform; avoidance of railroad reregulation; and reform of the Jones Act to improve global competitiveness. Quality Management is discussed in detail, including the techniques of Statistical Process Control and Total Quality Management.
Examinations
Completion of the certification program requires completion of an 80 question multiple choice examination prepared from the INTERNATIONAL SUPPLY CHAIN MANAGEMENT BODY OF KNOWLEGE. The examination is prepared by a Board of Examiners consisting of a range of Certified, Sustaining, and Educator Members within the three above Institutes/Societies.
The examination locations are determined by the individual candidates and their proctors. A proctor may be an individual who is currently an active Certified Member, or a manager, supervisor, teacher, professor, or anyone of such standing. Each proctor is determined on a case-by-case basis. IPSCMI wishes to make it possible for every qualified candidate to complete the certification program in a convenient and timely manner.
Minimum Requirements
Candidates who wish to become certified must meet the following requirements:
1. AA degree OR more than three years of experience in purchasing/supply chain management.
2. Satisfactory completion of a 3 hour multiple choice examination covering the INTERNATIONAL SUPPLY CHAIN MANAGEMENT BODY OF KNOWLEDGE (ISCMBOK) addressed in the training program.
3. Completion of an application for certification and payment of all fees.